
Industrial Digital Twin Solution
A Digital Twin is a virtual representation of a physical asset, process, or system, enabling you to monitor, analyze, and optimize your operations. By using an Industrial Data Fabric (IDF) solution and its components – Twin Talk, Twin Sight, and Twin Central – you can design and create a powerful and dynamic Digital Twin that provides real-time insights and supports advanced analytics and machine learning applications.
Twin Talk lays the groundwork for building your Digital Twin by providing secure, scalable data ingestion from SCADA systems and historians to the cloud. It removes the barriers associated with traditional data management systems, ensuring seamless data flow and integration for your Digital Twin.
Twin Sight offers an intuitive, user-friendly visualization tool and dashboard builder that allows you to access, analyze, and gain insights from the data captured by your Digital Twin. With real-time data at your fingertips, you can make timely, informed decisions and optimize your operations based on the digital replica of your assets.
Twin Central, the third IDF component, creates a comprehensive semantic data model for asset management in your Digital Twin. By linking, mapping, and managing all your metadata, Twin Central generates a single source of truth that unifies your entire organization’s data. This simplification of data management ensures efficient data access and streamlines analytics processes for your Digital Twin.
By leveraging the power of the IDF components, you can design a Digital Twin that serves as a valuable tool for monitoring, analyzing, and optimizing your assets and processes in real-time. A Digital Twin not only simplifies data management but also enables you to uncover new opportunities for improvement through advanced analytics, machine learning, and real-time data access. Embrace the potential of a Digital Twin created with IDF components to transform your operations and maintain a competitive edge in the ever-evolving industrial landscape.
Architecture for an Industrial Digital Twin with Twin Fusion
Designing and implementing an Industrial Digital Twin architecture with EOT products is a breeze, offering a simple, stable, and rapid solution. With no coding requirements or “Lift and Shift” components like AWS Lambda, AWS Glue, or AWS Kinesis, you can focus on creating a digital representation of your industrial assets. EOT’s clean, elegant, and highly performant architecture sets the industry standard, empowering you to optimize your operations and boost your business’s efficiency.
- Start by identifying specific use cases that provide real business value. Utilize Twin Central to create Assets and Data Models, which serve as the Single Source of Truth. This allows you to navigate through industrial assets within the Digital Twin, dashboards, and visualization apps.
- Based on these valuable use cases, use Twin Talk to configure Data Ingestion, Curation, and Contextualization. This enables the transportation and transformation of raw data from Data Sources into the data storage.
- With the selected use cases in mind, train and deploy Analytics and ML models to provide insights for the Digital Twin, dashboards, and visualization apps.
- Finally, use the Digital Twin, dashboards, and visualization apps to display operational, financial, and technical data, as well as insights from analytics and ML systems. This is all based on the specified use cases that drive real business value.
By following these four steps, you can effectively harness the power of an Industrial Digital Twin to drive meaningful insights and informed decision-making for your organization.
How to Get Started
The majority of digital transformation efforts fail due to one critical mistake: designing a logical architecture without a specific use case in mind. There are two common, but flawed approaches:
- Attempting to create an architecture that addresses all possible use cases for a company. This is often driven by business consulting firms that spend an excessive amount of time compiling use case lists involving the entire organization.
- Having no use case at all and adopting the mindset of gathering all data first, then discussing potential applications with users.
Both approaches almost certainly lead to costly projects that provide no value or support within the company and may even negatively impact the careers of project leaders. So, how should you get started? Select a use case that has two key attributes: 1) it’s quick to implement, providing a fast time-to-value, and 2) it delivers genuine business value for the company.
Enterprise Data Historian Features and Benefits

Overview
An industrial digital twin serves as a powerful tool for industrial companies by providing a single source of truth for asset metadata, asset relationships, and hierarchical structures. Here’s an in-depth look at how an industrial digital twin can be used by industrial companies with a focus on its role as the single source of truth for asset metadata, asset relationships, and hierarchies:
Centralized Asset Information
An industrial digital twin consolidates data from various sources, such as sensors, control systems, and enterprise software, into a single, unified platform. This centralization facilitates easy access to crucial asset metadata and ensures that all stakeholders have the most up-to-date information, streamlining decision-making processes and improving overall operational efficiency.
Asset Relationship and Hierarchy Management
Digital twins accurately represent the complex relationships and hierarchical structures that exist between assets within industrial environments. By visualizing these connections, organizations can better understand dependencies, identify potential bottlenecks or single points of failure, and optimize their processes for maximum productivity.
Performance Optimization
By serving as the single source of truth for asset metadata, digital twins enable organizations to continuously monitor and analyze asset performance in real-time. This insight allows for proactive maintenance, performance tuning, and process optimization, ultimately extending asset lifespans and reducing costs associated with downtime and repairs.
Predictive Maintenance
Industrial digital twins can leverage historical data and advanced analytics to predict equipment failure or degradation, allowing organizations to schedule maintenance more effectively and minimize unplanned downtime. This proactive approach results in lower maintenance costs, improved asset availability, and increased overall productivity.
Process Simulation and Optimization
Digital twins enable organizations to simulate different process scenarios and evaluate the potential impact of changes to their operations. By testing these scenarios in a virtual environment, organizations can identify the most efficient and cost-effective strategies before implementing them in the real world, reducing the risk of operational disruptions and ensuring optimal results.
Twin Fusion Components for Industrial Data Lake

EOT’s Twin Talk™ serves as a Data Integration Platform for industrial IoT, bridging the gap between operational systems (OT) and cloud (IT) solutions to unlock the untapped value of operational data. This innovative solution eliminates the complexity and costs associated with traditional infrastructure, enabling executives, operators, data scientists, and business analysts to harness AI, machine learning, and analytics for real-time insights and operational intelligence. Twin Talk streamlines the secure transmission of sensor data from assets while maintaining plant safety, allowing companies to focus on enhancing productivity through digitization and driving tangible business value.
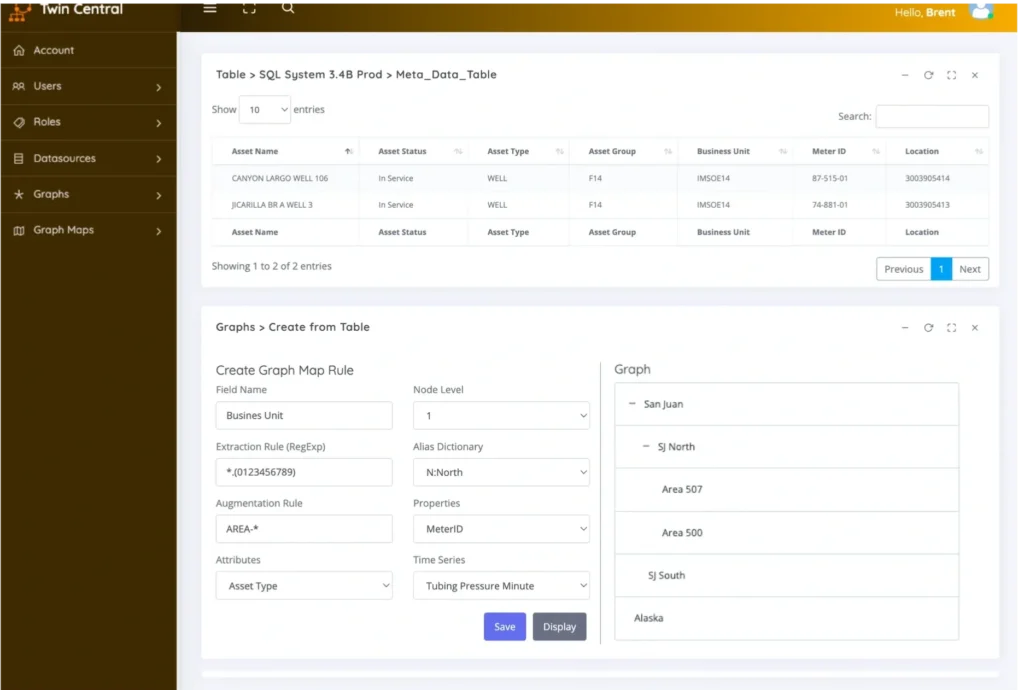
EOT’s Twin Central™ facilitates the creation of an asset-centric, single source of truth semantic data model. With Twin Central, business technologists can map, link, store, and synchronize relationships between assets and their operational, engineering, and financial metadata using a unified relationship graph. This straightforward approach enables the creation and management of an asset-centric, single source of truth and semantic data model across the enterprise. Twin Central allows for the development of digital twin data models that map, connect, link, store, and synchronize relationships between assets and their operational, engineering, and financial metadata using a unified digital twin relationship graph.

EOT’s Twin Sight™ offers a modern, rapid prototyping approach to operational dashboard authoring, accelerating the adoption of AI-based anomaly detection, production optimization, and operation monitoring across all production sites. With Twin Sight™, industrial users can leverage the power of low-code AI-driven software to modernize the visualization of asset information and data, driving the rapid creation of use-case-specific visual dashboards, templates, and reports. Twin Sight’s flexibility and ease of use enable any individual within the company to access enterprise-wide operational data through a self-service model and develop dashboards and reports tailored to their specific use case and business needs.